Many small motor applications, such as robotics, industrial equipment, and consumer products, employ digital incremental encoders for feedback sensing. Encoder selection is therefore an important part of the system design process. Choosing the best encoder for the job requires knowledge of the most important encoder properties as well as the application’s control requirements.
Each application is different; for example, the main task may be position control or speed control. The level of accuracy in speed or position control can be very different and should be defined before encoder selection. Speed control at low speed (below 100 RPM) needs a better feedback than speed control at high speed (1,000 RPM and above). Single Turn Multi Turn Encoder
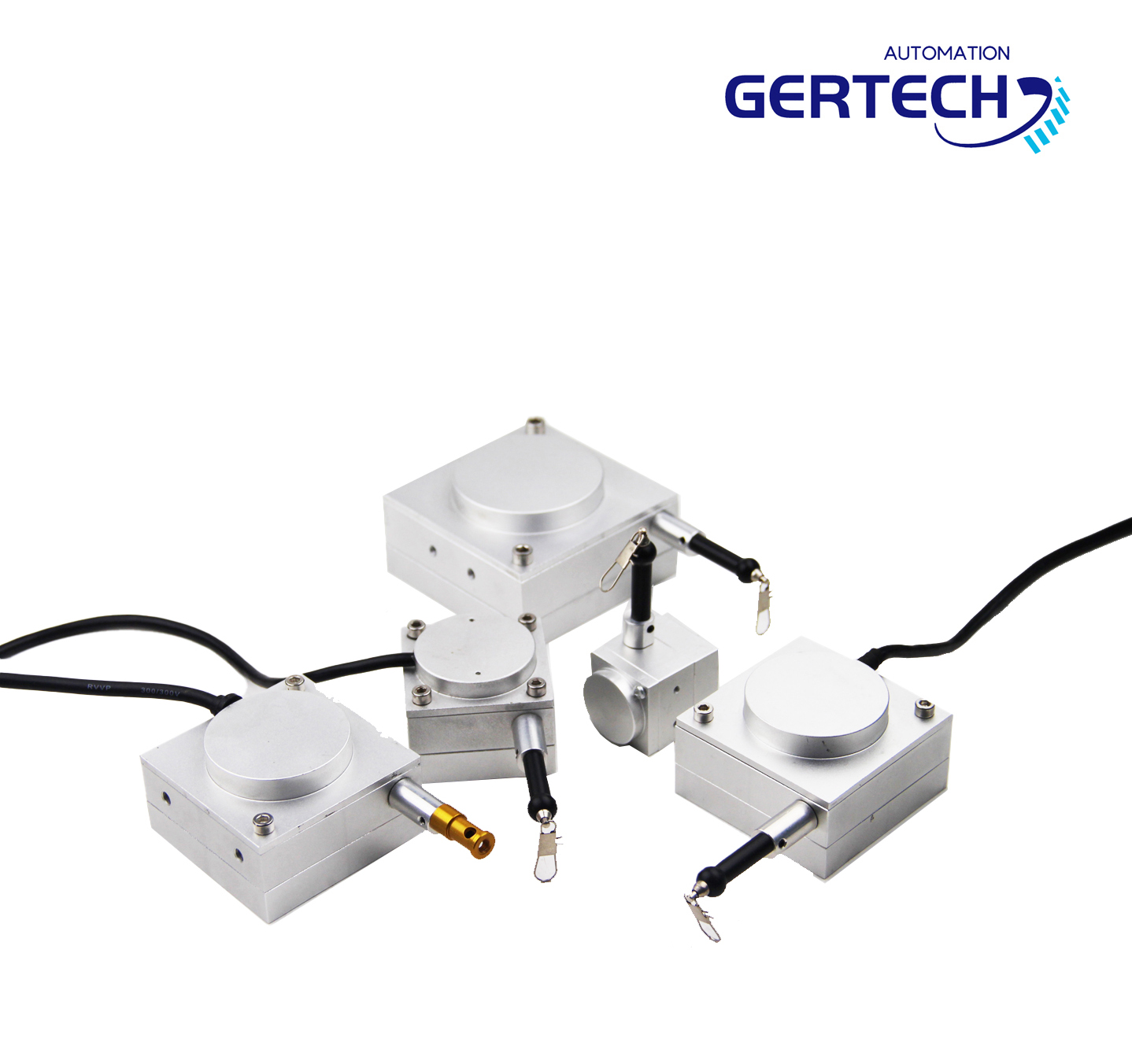
The load may be coupled directly onto the motor, or there could be a mechanical transformation system such as a gearhead or screws. Encoders typically are mounted on the motor shaft, but can also be on the load itself. The mechanical properties of the transformation mechanism influence encoder selection because gear reduction and mechanical play have to be taken into account.
Environmental conditions such as temperature, vibration, and electromagnetic interference may also have an influence on encoder selection. Optical encoders, for example, should be protected against dust. Magnetic encoders may be sensitive to external magnetic fields — including those of the motor — and may require shielding.
The characteristic parameter of an incremental encoder is the number of rectangular pulses per motor revolution. Typically, there are two channels delivering the same pulse number. The two signals have a relative phase shift of one quarter of a pulse length. This arrangement allows the detection of the direction of motor rotation and gives four distinct states per pulse. Sometimes these states are called quadcounts. They represent the real resolution, which is four times higher than the number of pulses on one channel (Figure 1). An encoder with 1,000 CPT (counts or pulses per turn) gives 4,000 states per turn, or a nominal resolution of 360°/4000 = 0.09°.
Encoder resolution spans a wide range from a very simple 1 CPT (or 4 states) encoder that can be used simply to detect motion, up to several 10,000 CPT for highly accurate position or speed feedback. There are many factors that influence resolution, including the underlying physical principle (optical, magnetic, inductive), the primary signal type (analog or digital), the signal treatment (e.g. interpolation), and the mechanical layout.
Resolution — the number of states — gives the nominal accuracy; the position is known within an error of one state. However, encoder pulse lengths may vary due to mechanical tolerances (e.g. shaft runout and length of magnetic poles). The pulses in one range of motor rotation may be shorter than the pulses of other ranges. As a result, the measured position deviates from the real position in a periodic way over one motor revolution (Figure 2).
The maximum deviation (peak to peak) is called integrated non-linearity (INL). INL is important in applications that require absolute position accuracy. Repeatability is not affected by INL, but is rather a question of signal jitter, and typically amounts to less than one state.
Incremental encoders give position changes. For absolute positioning, a reference or home position must first be established. This is achieved by moving the mechanism to an external reference that could be a mechanical end stop or a limit switch.
Some encoders feature a third channel with one pulse per turn. The edges of this index channel give absolute position references within one turn (Figure 3). The limited accuracy of external references can be improved by an additional move to one of the index channel edges. However, the index channel is not a prerequisite for positioning. In fact, machine builders try to avoid using the index for referencing because it requires new calibration if a motorencoder unit has to be replaced. Also, some controllers use the index channel to crosscheck the encoder signal and supervise the encoder counts per turn.
Line drivers are recommended for transmission over long lines and for better signal quality. For positioning, a line driver is important to avoid missing encoder pulses.
Line drivers generate inverted signals (A, B, I) for each channel (A, B, I). Each signal pair is transmitted together and the difference is evaluated, thus filtering out any electromagnetic interference during signal transmission. As a beneficial side effect, the signal quality is improved, the signal edges are more clearly defined, and the driver function enables the transmission of the signal over longer distances (up to about 30 m).
Encoders need a minimum supply voltage. On long encoder lines, the line resistance and the corresponding voltage drop can be an issue. That’s why it’s important to check the cable cross-section and the supply voltage.
The standard operating temperature range of encoders is in the range of –30 °C to +100 °C. This covers most of the applications and the heat produced by the motor. In applications with strong vibrations and with mechanical shocks, a robust mechanical housing and a good strain relief of the cables are important.
While optical encoders are less sensitive to electromagnetic interference, magnetic encoders need a good shielding against magnetic stray fields. If the housing is not sealed tightly, optical encoders are sensitive to dust.
The following basic rules can be used when selecting an encoder for positioning and speed control applications:
Rule 1: Encoder for Positioning — A good recommendation is to select an encoder with a number of pulses higher than 360° divided by the required angular position accuracy; in other words, a number of states that is four to ten times higher. For positioning, select an encoder with a line driver (differential signal).
Rule 2: Encoder for High-Precision Positioning — Select optical encoders with a line driver for high-precision positioning. They have a higher resolution, less jitter, and a lower INL than interpolated magnetic encoders.
Rule 3: Encoder for Positioning with Mechanics — Select a magnetic encoder with a line driver and with a moderate or low number of states. The mechanical reduction will increase the resolution. Due to the mechanical play, the system will not be able to benefit from a high-precision optical encoder.
Rule 4: Encoder for High-Speed Control (> 500 RPM) — Select an encoder with a moderate or low number of states and a sufficiently high maximum speed rating. There is usually not a need for a high-precision optical encoder. A good rule of thumb that is usually sufficient for most applications is (speed in RPM) × (encoder resolution in CPT) > 100,000.
Rule 5: Encoder for Low-Speed Control (< 100 RPM) — Select an encoder with a high or very high number of states in combination with a fast controller.
This article was written by Urs Kafader, Head of Training at maxon precision motors, Sachseln, Switzerland. For more information, Click Here .
To view the second part of this article, which covers encoder selection for position and speed control in more detail, go to www.techbriefs.com/encoder_selection.
This article first appeared in the February, 2017 issue of Motion Design Magazine.
Read more articles from this issue here.
Read more articles from the archives here.
Wi-Fi that Can Read Through Walls
New Hydrogel Uses Just Energy from Sunlight to Create Water
Quiz: How Much Do You Know About Wind Energy?
Here's an Idea: The Gripen E Jet's New Li-ion Battery
How Much Do You Know About Hypersonic Weapon Technology?
Here’s an Idea: Dr. Brendan Mulvaney Talks China’s Space and SATCOM...
Accelerate Electric Vehicle Development with HPC and Unified Design and Simulation
How Additive Manufacturing Can Increase Efficiency in EV Production
High Optical Power SOA and DFB Lasers for High Performance Photonic Systems
Integrating Thermal, Mechanical, and Fluid Dynamic Design Elements When Mitigating TRP
Precision, Control and Repeatability: Harnessing the Power of UV Curing in Medical Manufacturing
By submitting your personal information, you agree that SAE Media Group and carefully selected industry sponsors of this content may contact you and that you have read and agree to the Privacy Policy.
You may reach us at privacy@saemediagroup.com.
You may unsubscribe at any time.

Encoder Communication © 2009-2023 SAE Media Group