By Kurt Sassmannshausen, product development manager, System Seals
While nitrile butadiene rubber (NBR) has been a staple of wind-turbine seals for decades, advancements in polyurethane formulas, processing and seal design are quickly sidelining NBR’s place in the industry. The qualities proving most beneficial include abrasion resistance, fluid compatibility, ozone resistance, mechanical strength and the ability to maintain all these properties in low temperatures. High-Performance Timing Belt
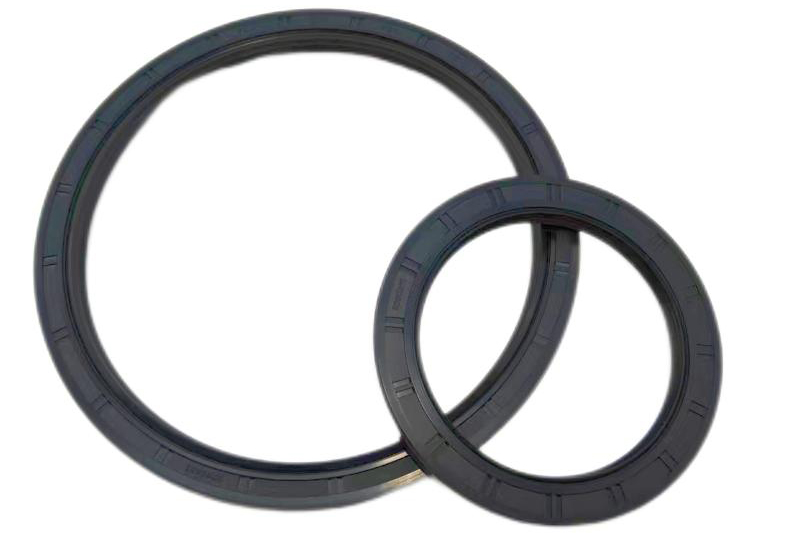
Polyurethane has emerged as an ideal material for seals in main/generator, pitch and yaw bearings. Nonetheless, simply swapping materials on existing designs often falls short. The seals must be engineered with polyurethane in mind.
One way to evaluate abrasion resistance in polyurethane is the standardized drum abrader test, such as ASTM D5963. This is often reserved for evaluating rubbers, but it is effective for polyurethanes as well, especially when comparing wear rates. Below are the abrasion-resistance-index values for various materials tested at System Seals in Cleveland. Note that while NBR and HNBR indicate ARI’s of ~1.5, polyurethane indicates an ARI of 4 to 8. This is an improvement of up to six-times.
Figure 1: ARI of elastomers and polyurethane
Polyurethane maintains its ARI value over time and after exposure to a wide range of fluids, most notably oil-based fluids. One way to determine this is to age ASTM D5963 abrasion samples in fluids for 90 days at 100°C (80°C for water-based fluids) and repeat the test every 30 days. Below are typical results, but confirmation for each fluid is recommended.
Figure 2: ARI retention of NBR and hydrolysis-resistant PU after ageing in distilled water at 80°C
Figure 3: ARI retention of NBR and hydrolysis-resistant PU after ageing in distilled mineral oil at 100°C
While spec sheets indicate out-of-the-box fluid compatibility, accelerated ageing tests – or years of application run time – should determine long-term performance and stability of a material exposed to a particular fluid. System Seals performs 90-day fluid compatibility tests, versus the industry-standard 168-hour tests, as System Seals has consistently found significant changes in critical material properties well after 168-hours of fluid contact.
Compared to NBR, custom-formulated polyurethanes demonstrate improved fluid resistance with the most common greases in the wind industry. Below is a compatibility chart for these popular greases.
Figure 4: Ageing scores in grease; lower is better
NBR is notoriously susceptible to ozonolysis – when ozone molecules separate the chemical bonds in unsaturated NBR. Ozone cracking is common when NBR experiences even minimal strains. One solution is to infuse NBR with waxes, which create an anti-ozone barrier that protects the NBR. Unfortunately, waxes do not change the chemical bonding of NBR. If NBR is exposed to environmental conditions that remove the wax, it again becomes susceptible to degradation. Some specialty polyurethanes used in wind energy seals are naturally ozone resistant.
Polyurethane has tensile modulus, strength and elongation two- to three-times higher than most NBRs. Because of this, polyurethane seals are capable of resisting greater mechanical deformation and sustaining higher mechanical loads.
A typical NBR has a tensile modulus of 10-15 MPa and a tensile strength of 20 MPa. Most polyurethanes have a modulus of 45-60 MPa and tensile strength of 50-60 MPa. This translates to a stiffer material that is less compliant than NBR, meaning greater shape retention under pressure and higher stress-load capability.
High temperatures are typically not a concern in wind applications. However, depending on location and elevation, -40°C minimum temperature is not uncommon. A minimum service temperature for standard NBR could be -20° C, while many wind-power polyurethanes are unaffected down to -40°C, as determined by dynamical mechanical analysis.
Figure 5: Comparison of glass transition temperature (Tg) to determine minimum service temperature
Figure 6: Radar plot of normalized property scores, higher is desirable
Polyurethane is a natural choice for wind-energy seals because it has greater mechanical properties, better ozone resistance, reduced wear rates and lower service temperatures. Below are two application families for which polyurethane is well suited. The left image shows simulated deformation and contact features of a polyurethane pitch bearing seal. The right image features System Seals’ Vortex seal, a main bearing seal that continuously pumps grease back into the reservoir at the bearing spins.
Figure 7: pitch seal FEA (left) and Vortex main bearing sea (right)
If you would like to contribute to Windpower, please contact us: https://www.windpowerengineering.com/meetourteam/
Browse the most current issue of Windpower Engineering & Development and back issues in an easy to use high quality format. Clip, share and download with the leading wind power engineering magazine today.

Cog Belts And Pulleys Copyright © 2023 WTWH Media LLC. All Rights Reserved. The material on this site may not be reproduced, distributed, transmitted, cached or otherwise used, except with the prior written permission of WTWH Media Privacy Policy | Advertising | About Us