Screwdriving is often the pacing procedure in the assembly process. Photo by Austin Weber
This screwdriving system provides precise control over speed, torque, axial force and stroke. Photo courtesy Deprag Inc. Automatic Screw Presenter
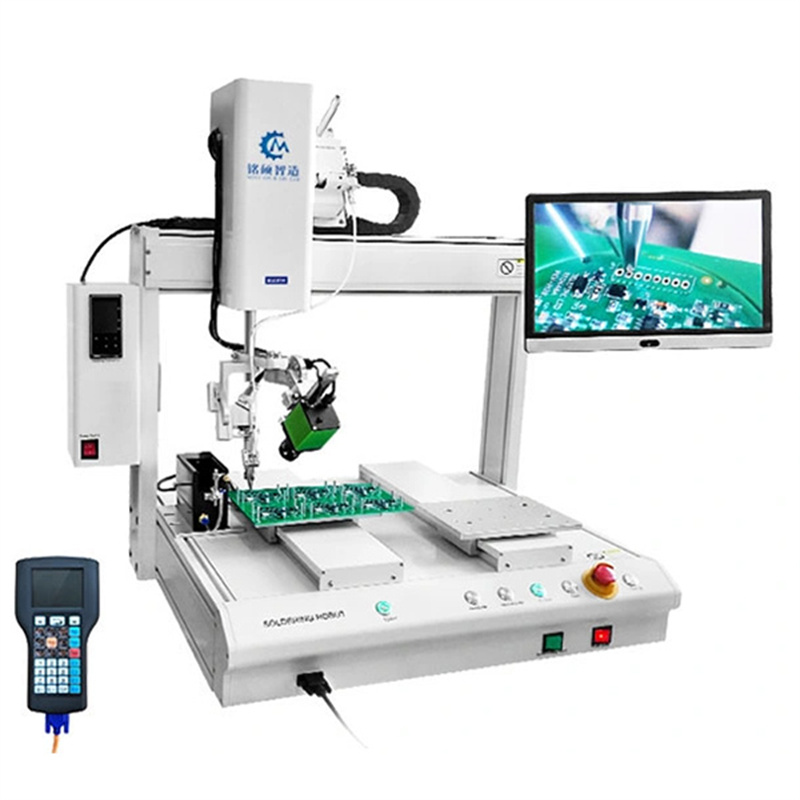
This current-controlled screwdriver can be used as a handheld tool, fixtured in a torque arm or mounted to an automated system. Photo courtesy ASG, Division of Jergens Inc.
This transducerized screwdriver allows engineers to control a variety of parameters during run-downs, including angle, running torque, clamping torque and total torque. Photo courtesy Kolver North America
Many manufacturers are investing in collaborative screwdriving systems that enable humans and machines to work in close proximity on assembly lines. Photo courtesy Visumatic Industrial Products Inc
Engineers must consider what screwdriving applications an operator can do better than a cobot. Photo courtesy ESTIC America Inc.
In most assemblies that are joined with threaded fasteners, the cost of the fasteners is not as important as the cost of installing them. Automation is one way to control that cost—but only if assemblers think ahead.
In that regard, assemblers must first decide if automation is even appropriate. Production volume is the primary consideration. But, because applications vary, it’s difficult to find a strict cutoff point at which automation makes sense.
In some cases, manufacturers can justify the cost of automation with less than 1,000 screws per shift. The average assembler probably installs 4,000 screws per shift.
Screwdriving experts estimate that 500,000 screws installed annually is a good starting point for considering a handheld system with an automatic screwfeeder. Such a system can install small screws at a rate of one per second. A fully automatic system can perform 20 to 40 insertions per minute per spindle.
Most systems are purchased to increase productivity rather than just reduce labor cost. Screwdriving is often the pacing procedure in the assembly process.
The decision to automate screwdriving often depends on what other tasks the operator must perform. Usually, operators have to assemble the parts, in addition to driving screws. If they spend 90 percent of their time assembling parts, and only 10 percent driving screws, then a screwfeeder doesn’t make sense. If screwdriving time goes up—if there are multiple screws on a part—then it makes sense to use a screwfeeder.
Besides volume, labor costs and productivity, other factors can help justify investment in automatic screwdriving equipment. Ergonomics is one such factor. Product quality is another. Because machines are simply more reliable than people, automation can increase quality.
Depending on how they feel on a given day, operators may or may not be interested in installing screws correctly. They can release from a joint early, and no one would be wiser until quality control caught the problem. In contrast, a machine will install screws exactly the same way every time.
Compared with human operators, machines are much better at keeping the driver vertical. That’s particularly important with self-tapping screws. It’s critical that this fastener be inserted straight into the hole. If it’s leaning to one side or the other, the fastener tends to cut its way in crooked. By controlling all three axes, a robot eliminates the human variable.
Simply controlling how fasteners are presented to the operators can sometimes be enough to justify the cost of automation. An automotive assembly plant learned that lesson a few years ago. To assemble dashboard instrument panels, operators manually inserted screws and tightened them with handheld power tools. Inevitably, a screw would get lost inside a dashboard, causing an annoying rattle.
The problem was costing the automaker thousands of dollars in warranty claims each year. A simple screwfeeder allowed engineers to control and account for fasteners and saved the company a lot of money.
Ironically, the most important part of an automatic screwdriving system often gets the least attention—the fastener itself. According to screwdriving system suppliers, the best screws for automation are those with internal drive recesses, such as Phillips, Phillips ACR, Torx and Torx Plus. Driver bits are less likely to cam, or slip, out of screws with internal recesses.
Those screws perform better in automated assembly systems, because the bits line up and stay within the centerline of the fastener. Slotted screws are difficult for most machines to deal with, because the bit falls out so easily.
Hex-head screws also work well with automatic screwdriving equipment. However, engineers should be sure to provide extra room around the fastener, to account for the size of the socket.
The head style of the fastener is important for reliable feeding. As fasteners exit a feeder bowl, they are confined by a pair of rails. The screws then push against each other on their way to the feed tube. Pan heads, cylindrical heads and other styles with good "pushing" surfaces work the best in this type of arrangement.
The larger the contact surface between screws, the better. Countersunk screws have a very small area where they hit each other, and they tend to shingle and climb up on top of each other in the feed rail.
For reliable feeding, the overall length of the screw must be greater than its diameter. A good rule of thumb is that the ratio of the head diameter to the length should be at least 1-to-1.5. Otherwise, the screw will tumble in the feed tube. If the screw has an even aspect ratio, it can’t be blow-fed it. It has to be fed on a track to the point of insertion.
The shape of the screw point is also important. A dog point, which helps guide the screw tip into the part, is very effective.
A difficult, but not impossible, feeding job is a screw with a preassembled washer. Ideally, the washer should sit right under the screw head, but often it threads itself down the shank, which can cause problems with automatic feeders. The solution is to add a mechanism that taps down on the fastener while it is on the feed rails. This will push the washer back up under the head.
Coatings are a more problematic fastener add-on. Grease, wax and other fastener coatings can leave sticky deposits inside feeder bowls and rails. These deposits must be cleaned periodically to ensure reliable feeding.
Finally, assemblers are well-advised to invest in high-quality screws, regardless of their size, shape and style. Every misformed screw is a potential jam. The whole line could come to a stop because of one bad screw, so quality screws are always recommended. It will cost a little more per 1,000 fasteners, but your downtime will be less. It will pay back on the other end.
Just as quality screws will pay dividends with automation, so too will quality parts. Unlike people, machines can’t compensate for slight variations in hole locations or parts positioning. Rather, machines are designed to install screws in a specific location time after time—regardless of whether a hole is there or not.
When designing parts for automatic screwdriving, engineers should make sure that the driver head has a good approach angle to the parts. They should also provide enough clearance around each fastening location for the driver head to fully seat the screw.
Flexibility requirements are another issue that should be addressed early in the design stage. Automatic screwdriving equipment can be built to accommodate different fastener sizes and product configurations. But, flexibility may involve trade-offs in speed or price.
Consider, for example, a product that requires four identical screws to be installed in the same plane. At the right volume, the most economical solution might be to mount four automatic screwdriving spindles in a steel plate attached to a linear actuator. But, if the hole pattern changes, the mounting plate, and perhaps even the actuator, will have to be remade, which could be time-consuming and expensive. If change is expected, a better alternative might be one or more single-spindle systems mounted to an XYZ positioning system.
Similarly, by standardizing the fasteners used in different products, assemblers can decrease the initial cost of automatic screwdriving equipment and prolong the return on investment period. One screwdriving supplier built an automated assembly system that handled seven different screws. The fasteners were different lengths, and some even had different drive recesses. By reducing the number of different screws used in its products, the customer might have lowered the cost of the assembly machine.
Automatic screwdriving machines can be equipped with electric or pneumatic tools. For general assembly work, pneumatic tools are preferred for their durability and high power-to-weight ratio.
For low-torque applications, a brush DC electric tool is often preferred. Some assemblers want torque and angle measurement from the tool for statistical process control. In this case, a brushless DC electric tool with a transducer and encoder is used.
With the right tooling, torque control with an automatic system should be as good as with a manual tool. However, engineers may need to adjust their torque specifications to allow for the drag as the bit and fastener exit the jaws of the machine.
Electric or pneumatic, every automatic screwdriving system requires regular maintenance for dependable operation. For example, driver bits should be replaced according to a regular preventive maintenance schedule, instead of only when they break. As with fasteners, assemblers will save money in the long run by investing in high-quality bits.
Bits are typically softer than the screws they drive, and they are often bought on the cheap. Assemblers should be able to get 10,000 to 15,000 parts out of one bit.
Screwdriving tends to be a dull, repetitive task for humans, making it prone to errors. It’s a perfect candidate for collaborative robots, which can provide flexibility and repeatability.
Faced with severe labor shortages and reshoring initiatives, large and small manufacturers are investing in collaborative screwdriving systems that enable humans and robots to work in close proximity on assembly lines.
Operators can work side by side with cobots. Humans can focus on tasks that are easily accessible, while the machines work on things that are more difficult, such as inserting and driving screws in hard-to-reach areas or confined spaces where fasteners aren’t always visible.
“[Automated] screwdriving used to be a task that was complex, costly and took up a large footprint on the assembly line,” says Catherine Leclerc, product owner for screwdriving applications at Robotiq Inc. “As such, it was reserved for use in vast plants with big automation budgets producing in high volumes.
“This type of custom project by an integrator could hardly meet the reality of small manufacturers that deal with [limited] assembly line space, tight budgets and [sparse] automation staff,” Leclerc points out. “Now, with screwdriving systems designed specifically for cobots, the technology has become accessible to any manufacturer.
“There are screwdriving systems that can be bought off the shelf, shipped within a few business days, easily installed and adapted to production changes,” claims Leclerc. “It’s a completely new era.”
“Screwdriving is a great application for cobots,” adds Joe Campbell, senior manager of strategic marketing and applications development at Universal Robots, the company that pioneered the technology more than a decade ago. “In fact, it’s one of our most popular applications.
“All of the programming is done through the UR teach pendant,” Campbell points out. “That has simplified things and removed a lot of risk, especially for smaller manufacturers that may have shied away from automation in the past.”
Collaborative screwdriving is used in many industries. However, engineers must perform a thorough risk assessment and deploy proper safeguarding to ensure the safety of humans working around or with a cobot.
“Every company is different in how they determine what ‘collaborative’ means and how they set up in-house rules of engagement,” adds Jarrod Neff, marketing manager at Visumatic Industrial Products Inc.
“We have some customers that use cobots in conjunction with light curtains, safety guarding or area sensors that can detect human movement,” says Neff. “They want higher throughput, but simply don’t feel comfortable operating their machine at maximum speed.”
According to Neff, cobots are popular for driving small screws that range in size from M1 to M3. “Typically, screws with lengths up to 20 millimeters work best,” he points out.
“Cobot screwdriving requires slower movements, lower throughputs and lighter duty tooling on the end of arm,” claims Neff. “As a general rule of thumb, any application that requires a torque of 50-inch-pounds or less, should be OK to use with cobots,”
“[Using] safety-caged, fully automated [screwdriving] is typically expensive, complicated and maintenance intense,” adds Don Seay, general manager at ESTIC America Inc. “Engineers can now take a hybrid approach and consider which assembly processes are best served by an operator, and what processes could be performed by a torque tool integrated on a cobot working beside a human.
“Engineers need to consider what applications an operator can do better than a robot,” explains Seay. “Then, assign tasks to the machine that would make the human’s job easier. You might see humans do hand starts of screw, with cobots doing final tightening with a torque tool down the line. That allows cycle times for humans to be faster.”
You must have JavaScript enabled to enjoy a limited number of articles over the next 30 days.
On Demand Connecting shop floor tools to a manufacturing execution system is critical to error-proofing assembly processes, improving quality control, and lowering defect and scrap rates. Join Torrence Williams, Partnerships Manager for Pico MES, and Dan Smith, VP of Sales for Kolver Tools, as they discuss an easier path for manufacturers to start connecting their factory floor.
On Demand This topic is something that challenges each of us every day that we go to work. This talk is about change and why it works and why it fails. It is focused on manufacturing facilities, because that is where the author has spent most of his working life.
Copyright ©2024. All Rights Reserved BNP Media.

Screw Feeding Machine Design, CMS, Hosting & Web Development :: ePublishing