Injection molding is the obvious onward step from 3D printing when the making of a few plastic parts becomes their series manufacture. The problem with injection molding is though, that making a mold can be prohibitively expensive. Has the advent of affordable CNC machining changed that? [Teaching Tech] takes a look, and machines a mold for part of a bicycle bracket.
With a diversion into home-made silicone seals for the injection molding machine, he proceeds to machine the mold itself from a block of aluminium. It’s a basic introduction to mold construction for those of us who’ve never ventured in this direction before, and it provides some interesting lessons. As we’d expect he does a rough machining pass before returning with a ball-end tool to smooth off those curves, but there’s a lesson in measuring rather than believing the paperwork. The tool he used was a bit smaller then the spec, so his path left some rough edges that had to be returned to. Otherwise the use of a removable pair of bolts to form holes in the finished part is we guess obvious after watching the video, but it’s something we learned as injection molding newbies. Side Core Mold Design
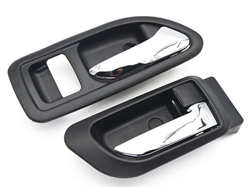
This video follows on from a previous one we also covered, in which we’re introduced to the machine itself.
No ejection pins/sleeves. Parting line through the gate. Bolts as alignment pins. Huge vents drilled by hand. This is clearly his first injection mold.
He’d have been much better off just machining the bracket. Cycle time will be measured in days. Bet he ruins the mold, prying out a short shot with a hard steel screwdriver.
Heaven forbid people try stuff on their own for the first time, and learn stuff in the process. Pack it up boys! Learning is forbidden now!
There are books. You can avoid making the same old mistakes made by others. He’s not inventing anything, well trodden path.
2 years in the lab can save you 15 minutes in the library!
why don’t you contact him and share your knowledge or improve his design?
why so “pro” have to act like jerk in comments? do you feel threatened ? had is about hacks and diy, if you come here to show off – in comment section, go elsewhere.
All of their smug assumptions is what really pushes me over. It wouldn’t really be worthy of HaD if it was a perfectly polished and professional project, would it? It’s a hack job? Great! Getting the job done is what matters.
I think you are missing the idea behind the comment. Designing molds is already out there. The comment is directed at the point of you are wasting time and energy making screw ups instead of reading, reading is learning, then apply those concepts that are proven to work to your project. And to research the Wikipedia for the correct answer instead of a book on injection molding. Says what about the general concept that everything on the web is correct lol.
You missed the point, read first, then proceed to the project.
And they’d all be better off just making the part. Single use molds are stupid.
And where are your 452k aubscribers?
You mean the right things but you say the wrong things.
He’s a libertarian, what do you expect when his brain is still to develop.
Of course he doesn’t actually know what a libertarian is, making him a true libertarian. (I wonder how Scottish libertarians get on.)
I’m sure he understands better than you it’s his first. Prototype, find failure, improve. Idk wtf your thinking really. Your argument is obviously one from someone that lacks the “doing” or non of this would be off putting to you.
yeah your comment is what i read the article for. when i read make an injection mold out of aluminum i knew the interesting story would be its shortcomings. the next part to complete the article would be a description of how useful it was despite those shortcomings. but i’m not about to watch a youtube video so
There would be less short comings if he had read some books. I bet he doesn’t even know what a tolerance analysis is! It’s more about being on you tube then it is about learning, doing, showing. Instead it’s about showing doing, learning, which is backwards. When you are doing something no one else has done them is the other way around, because you have to experiment to figure out of. When it’s a known methodology it’s learn do and show.
I have been tempted to try injection molding, as I do have a small CNC milling machine and a fair bit of casting experience. The main thing still putting me off is the cost & size of equipment to produce anything over a couple of cm^3, but as soon as I can find a commercial justification I’ll be all over it.
I used to be put off by the need for metal tools, but it seems like you can get good results using a metal box with RTV silicone inserts – there’s a few videos about that on the “Crafsman SteadyCraftin” YT channel. Since you can make silicone negatives from anything (3D prints, machinist’s wax, clay…), you could combine the productivity of injection molding with fast iteration, which for me would make up for the shorter life of the tool. Plus, you’ll never get a part stuck in a silicone mold.
Injection molding machines are deceptively dangerous, which is why we expunged our groups linear-actuator based hobby project (roughly 800psi with a 1200W pre-melt zone).
You may be surprised to learn a used surplus professional unit is often under a few thousand dollars, but just like a big iron knee mill the freight is ridiculous. Have a look for local industrial equipment liquidators if you have 3-phase power, and a hot-air plastic pellet dryer to help prevent steam ruptures.
Note, get the seller to quickly show you how a unit works if possible. The timing/material/process data they share for that specific machine could save you a lot of time, money, and frustration.
Also, factory machine brands/models have specific mold mounts, as such they are often a cu$tom part.
I’ve always suspected that’s because unlike electricity we just don’t get the danger of pressure drilled in. I’ve stopped people from learning a hard lesson with pressurized vessels a few times.
In any industrial setting you will eventually meet all sorts of people missing fingers, arms, an eye, and or legs. The worst I saw in school was a kid that had scar tissue from her shoulders to the top of her face… from a “small” ram injection molding machine shop accident (the pneumatic piston that drove the ram stayed intact, as steam just launched it back out as it was ripped off a 1/4” aluminum plate).
Much like the Precious Plastic and the unit in this article, the machine we had in the schools shop was not enclosed in a blast-shield from the factory. Incidentally, out of ignorance people often did not respect the procedure to drive off water until after a failed run, and PPE/face-shield at the time only saved half her face. (Napalm victims looked similar.)
Kids tend to ridicule the precautionary policy of people that have decades of training while working in labs and shops. However, many also wrongly assume YT video-editors are not in a Darwinian zero-sum Game, and that controversy drives engagement stats.
HaD has gone “full-retard” from my perspective.
Take care of yourselves, and have fun. =)
Any sufficiently interesting project usually has the potential for maiming or killing me. That’s part of the fun. If safety came first, we’d all be paper pushers. No thanks.
Look up “Precious Plastic” on youtube. They’ve made a manual injection molder from pipe fittings with a fairly huge shot size. Seems easy enough to build.
I’ve duplicated an Ethernet cable’s injection-molded semi-flexible strain relief with a Lego mold box, silicone molding putty, and a hot glue gun.
Air bubbles and mold erosion were definitely present, but the end result was far nicer than all slip-on style strain reliefs I’ve encountered, and it held up enough for the half-dozen cable ends I needed to produce.
??? Once you have made an injection mold for yourself, then how do you inject yourself into that mold? Injection needles are probably all far too thin. Maybe it can work when combined with a hydraulic press. There is a channel where they can do nearly anything with a hydraulic press. Maybe it’s possible to turn an ejection seat into an injection seat, but I can already feel a headache coming by just thinking about it. And executing the plan could also easily give a much more severe headache.
Comedy really isn’t your thing.
This is the worst comment I’ve ever read anywhere.
I have a great deal of machining experience as well as die making, and I’ve considered at some point making an injection mold for polycarbonate, only because I would like face form fitting a safety glasses as close to my eyes as possible. I do a lot of micro work and I have a flip down lens that I leave on my safety glasses, but I bring my head close to a lathe headstock. The safety glasses I use for this are rather expensive Smith & Wesson phantoms, I actually have a 3D scanner and I’ve been tempted to just scan my face and mold glasses that follow the curvature of my face.
And then I remember there is a ton of difficulty behind the injection molding part and I give up, haha.
I would suggest [JohnSL] has a better series of videos covering garage-scale injection molding. https://www.youtube.com/@JohnSL
Please be kind and respectful to help make the comments section excellent. (Comment Policy)
This site uses Akismet to reduce spam. Learn how your comment data is processed.
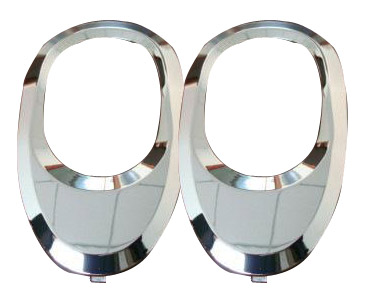
Hasco Mold Manufacturer By using our website and services, you expressly agree to the placement of our performance, functionality and advertising cookies. Learn more