A mainly sunny sky. High 63F. Winds NNW at 5 to 10 mph..
A mostly clear sky. Low 39F. Winds light and variable. T24 Brake Chamber
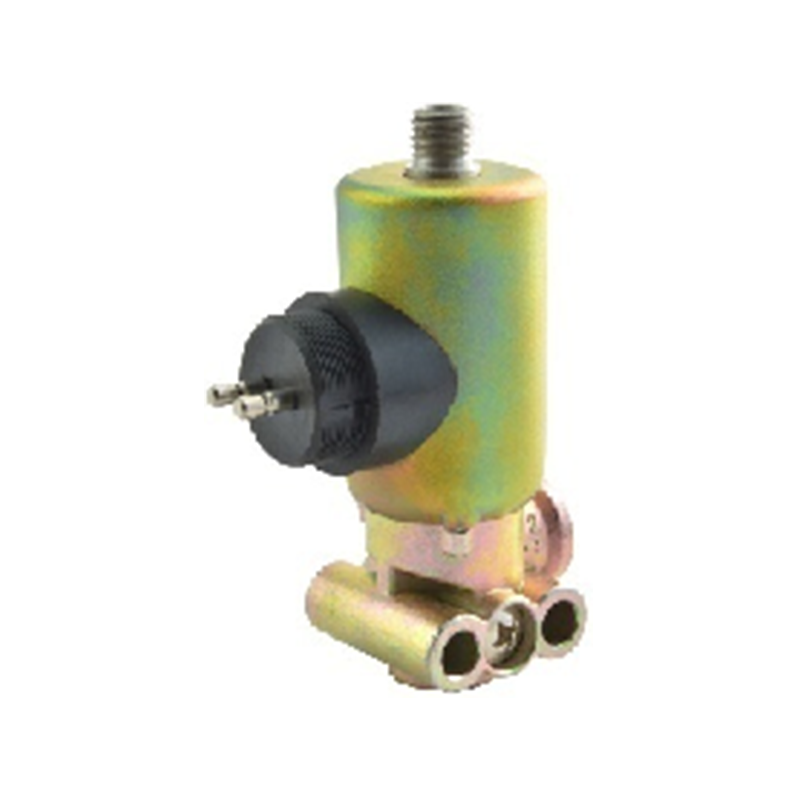
In the world of automation and control systems, the choice between pneumatic and electric valve actuators can be a pivotal decision, determining the efficiency, reliability, and cost-effectiveness of your processes. It's a bit like choosing between two superheroes, each with its unique set of powers and capabilities.
So, whether you're a seasoned engineer looking to fine-tune your system or a newcomer navigating the complex world of valve actuation, join us on this journey as we explore the battle between pneumatic and electric valve actuators, helping you discover which one is the true hero for your specific needs. Strap in, because it's time to unleash the power of fluid dynamics and electrical precision in the ultimate showdown!
Are you looking for a reliable and cost-effective solution to control valves in your industrial processes? Pneumatic valve actuators might be the answer you need! Discover the benefits of pneumatic actuators and learn why they could be the perfect fit for your applications. Take the first step towards improved valve control with pneumatic technology.
Pneumatic valve actuators are devices designed to control the opening and closing of valves by using compressed air or gas to create mechanical motion. These actuators are commonly used in various industrial applications, where precise and reliable valve control is essential. The basic working principle of pneumatic valve actuators involves the conversion of pneumatic energy into mechanical force to operate a valve. When compressed air or gas is supplied to the actuator, it enters a chamber, causing a piston or diaphragm to move. This movement is then transferred to the valve stem, which, in turn, opens or closes the valve. Pneumatic actuators can operate in both linear and rotary motions, making them versatile for different valve types and applications.
Pneumatic valve actuators offer several advantages in various industrial settings. Firstly, they are known for their rapid response and high-speed operation, making them suitable for applications that require quick valve adjustments. Additionally, pneumatic actuators are relatively simple to install and maintain, reducing downtime and operational costs.
They are also resistant to overloads and can handle heavy-duty applications, making them suitable for large valves and industrial processes. Furthermore, pneumatic actuators are intrinsically safe in hazardous environments, as they do not produce sparks or electrical discharges. Their reliability and durability make them a preferred choice in industries such as petrochemical, pharmaceutical, and wastewater treatment.
Despite their advantages, pneumatic valve actuators have certain limitations. One significant drawback is their dependency on a source of compressed air or gas, which requires the installation of additional equipment like compressors and pipelines. This dependency can result in higher energy consumption and operational costs compared to electric actuators.
Pneumatic actuators may also experience issues with air leaks or contamination, affecting their precision and efficiency. Moreover, their control and positioning accuracy may not be as high as electric actuators, making them less suitable for applications that demand extremely precise control, such as in the aerospace or semiconductor industries.
In the ever-evolving world of valve control technology, electric valve actuators, including Honeywell valve actuators, are gaining popularity for their precision and efficiency. If you're seeking a cutting-edge solution, explore the advantages of electric actuators, such as Honeywell valve actuators. Find out how these advanced actuators can revolutionize your valve control systems. Embrace the future of valve automation today!
Electric valve actuators, including Neptronic valve actuators, operate by converting electrical energy into mechanical motion. They consist of an electric motor, a gearbox (for rotary motion), and a drive mechanism that connects to the valve stem. When electrical power is applied to the motor, it generates rotational or linear motion, depending on the actuator type. This motion is then transmitted to the valve stem, causing the valve to open or close. Electric actuators, such as Neptronic valve actuators, offer precise control and positioning capabilities, making them suitable for applications that require accurate regulation of flow, pressure, or temperature.
Electric valve actuators, including spring return valve actuators, offer several advantages that make them a popular choice in various industries. Firstly, they provide precise and repeatable control, allowing for fine-tuning of valve positions. This level of control is crucial in applications like HVAC systems, water treatment plants, and food processing, where maintaining specific conditions is essential.
Electric actuators are also highly reliable and require minimal maintenance, leading to reduced downtime and operational costs over time. Furthermore, they do not rely on external air or gas sources, eliminating the need for additional infrastructure, and are suitable for indoor and outdoor use. Additionally, electric actuators are often quieter and produce fewer vibrations compared to pneumatic actuators, which can be advantageous in certain applications.
While electric valve actuators offer many benefits, they are not without drawbacks. One limitation is their potentially slower response time compared to pneumatic actuators, which may not be suitable for applications that require rapid valve adjustments. Electric actuators can also be more expensive to purchase upfront than their pneumatic counterparts.
However, their lower operational and maintenance costs often offset this initial investment in the long run. Electric actuators may also require more complex control systems and electrical wiring, which can be challenging to set up and troubleshoot. Additionally, in hazardous environments, electric actuators may require special enclosures to protect them from adverse conditions or potentially explosive atmospheres.
Choosing the right actuator for your application, whether pneumatic or electric, requires careful consideration of several factors:
Application Requirements: Understand the specific needs of your application, such as valve size, torque or force requirements, and speed of operation.
Environmental Conditions: Consider the operating environment, including temperature, humidity, and potential exposure to corrosive substances, as this can impact the choice of actuator.
Energy Source: Determine the available power source. Electric actuators are often more versatile in this regard, while pneumatic actuators require compressed air.
Control System: Evaluate the control system compatibility. Electric actuators offer precise control options, while pneumatic actuators may require additional accessories for fine-tuned control.
Maintenance: Consider the maintenance requirements of each type. Pneumatic actuators are generally simpler to maintain, while electric actuators may require more attention.
Cost: Compare the initial cost and long-term operating expenses of both options, including installation and energy costs.
Safety: Assess safety considerations, such as the risk of electrical hazards with electric actuators and the potential for leakage in pneumatic systems.
Size and Weight: Account for space constraints and weight limitations, as electric actuators can be bulkier and heavier than pneumatic ones.
Scalability: Think about future scalability and potential changes in your application's requirements.
Ultimately, the choice between pneumatic and electric valve actuators will depend on your specific application's needs and constraints. Carefully weigh these factors to make an informed decision that ensures optimal performance and efficiency.
The choice between pneumatic and electric valve actuators ultimately depends on your specific needs and requirements. Pneumatic actuators offer simplicity and reliability, making them a cost-effective choice for many applications. On the other hand, electric actuators provide precise control and flexibility, making them ideal for complex systems that demand accuracy and automation.
It's essential to carefully assess your project's parameters, including budget, control requirements, and environmental factors, before making a decision. By doing so, you can ensure that you select the right valve actuator technology to optimize the performance and efficiency of your system.
The Role of Linear Actuator Motors in Smart Devices
How Do I Start Automate My Home?
Hydraulic Cylinder Repair: When to Replace and When to Repair?
Your comment has been submitted.
There was a problem reporting this.
Keep it Clean. Please avoid obscene, vulgar, lewd, racist or sexually-oriented language. PLEASE TURN OFF YOUR CAPS LOCK. Don't Threaten. Threats of harming another person will not be tolerated. Be Truthful. Don't knowingly lie about anyone or anything. Be Nice. No racism, sexism or any sort of -ism that is degrading to another person. Be Proactive. Use the 'Report' link on each comment to let us know of abusive posts. Share with Us. We'd love to hear eyewitness accounts, the history behind an article.
Sorry, there are no recent results for popular videos.
Sorry, there are no recent results for popular commented articles.
Sorry, there are no recent results for popular videos.
Sorry, there are no recent results for popular commented articles.

Long Stroke Brake Chamber Your browser is out of date and potentially vulnerable to security risks. We recommend switching to one of the following browsers: