RJG has augmented its CoPilot process control with artificial intelligence (AI) trained on in-house data gleaned from its network of training labs.
RJG has added MAX — an AI-powered process advisor — to its CoPilot process control system. RJG says MAX, short for Molding Automation Xperience, uses AI technology powered by proven Master Molder techniques to provide molders with real-time guidance for optimizing their injection molding processes. Silicone Prototype
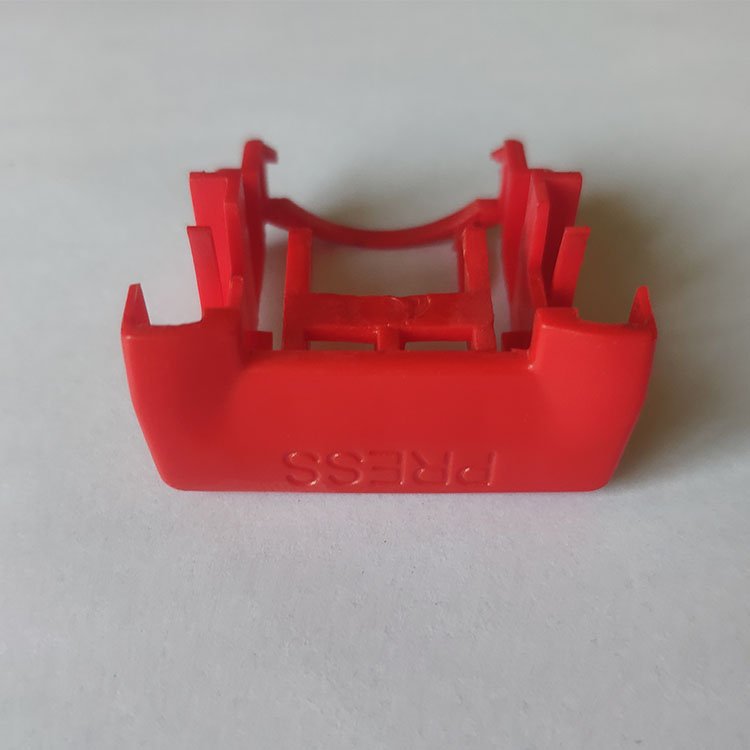
An RJG spokesperson told Plastics Technology that the AI runs locally on the CoPilot and was trained on data from multiple sources, including the company’s in-house CoPilot data and the expertise of its trainers, which it says ensures that MAX adheres to how RJG teaches, matching a template in its Master Molder courses.
The company used its Traverse City, Michigan, lab machines and molds for a period of months working with internal subject matter experts, trainers and outside consultants. The spokesperson said RJG also used its training labs in the U.K., France, Alabama and North Carolina, leveraging their in-house experts and trainers to test the system. In addition, it was beta tested at two external partners, beginning in October.
RJG notes that molders face a shortage of skilled processors who can troubleshoot injection molding processes, resulting in excessive scrap, machine downtime and wasted engineering hours. RJG developed MAX to assist in bridging that skills gap and reducing waste during production.
The smart assistant monitors process parameters in real-time and offers troubleshooting advice to help molders resolve issues and improve productivity. Featuring an intuitive interface, MAX delivers step-by-step instructions for restoring a process to an optimized state. When a process goes out of match, the technician is alerted by the card-select icon that there’s an issue. Tapping this icon takes the technician to the card-select screen, where the template match card is highlighted, prompting the technician to tap it. Once clicked, the job dashboard rearranges to display the most helpful data and start to get the process back into match.
On the CoPilot’s job dashboard, technicians can view the guidance system card, enabling them to verify that the machine settings match the setup sheet. Technicians then indicate whether each setting matches, if it’s been fixed or if it does not apply to this process. Once the settings are confirmed, the system waits 30 minutes for the process to stabilize before giving the technician more advice.
Upon stabilization, the guidance system will continue advising the technician based on decoupled molding principles, recommending process adjustments in a systematic manner. After an adjustment has been made, the system waits a total of three cycles for the process to stabilize, before offering additional advice.
The guidance system continues this cycle of advice until the process is stabilized and the template is once again matching. Once the guidance is complete, the technician can document what was done in a note. By documenting the problem — including what changes were made and by whom — CoPilot helps ensure transparency from shift to shift, keeping a record of what was changed and when.
MAX, short for Molding Automation Xperience, uses AI technology powered by proven Master Molder techniques. Photo Credit: RJG
Five industry pros with more than 200 years of combined molding experience provide step-by-step best practices on mounting a mold in a horizontal injection molding machine.
Modifications to the common core pin can be a simple solution, but don’t expect all resins to behave the same. Gas assist is also worth a try.
Weld or knit lines are perhaps the most common and difficult injection molding defect to eliminate.

Titanium Part Machining © 2023 Gardner Business Media, Inc. Privacy Policy [Log On]