In this Ask the Experts feature, expert instructors from the Compressed Air Challenge (CAC) will tackle your questions on compressed air systems and associated technology.
The Compressed Air Challenge is a voluntary collaboration of industrial end-users; manufacturers, distributors, and their associations; trade organizations; consultants; state research and development agencies; energy efficiency organizations; and utilities. The CAC has one purpose in mind; helping you enjoy the benefits of improved performance of your compressed air system. Industrial 12v Air Compressor
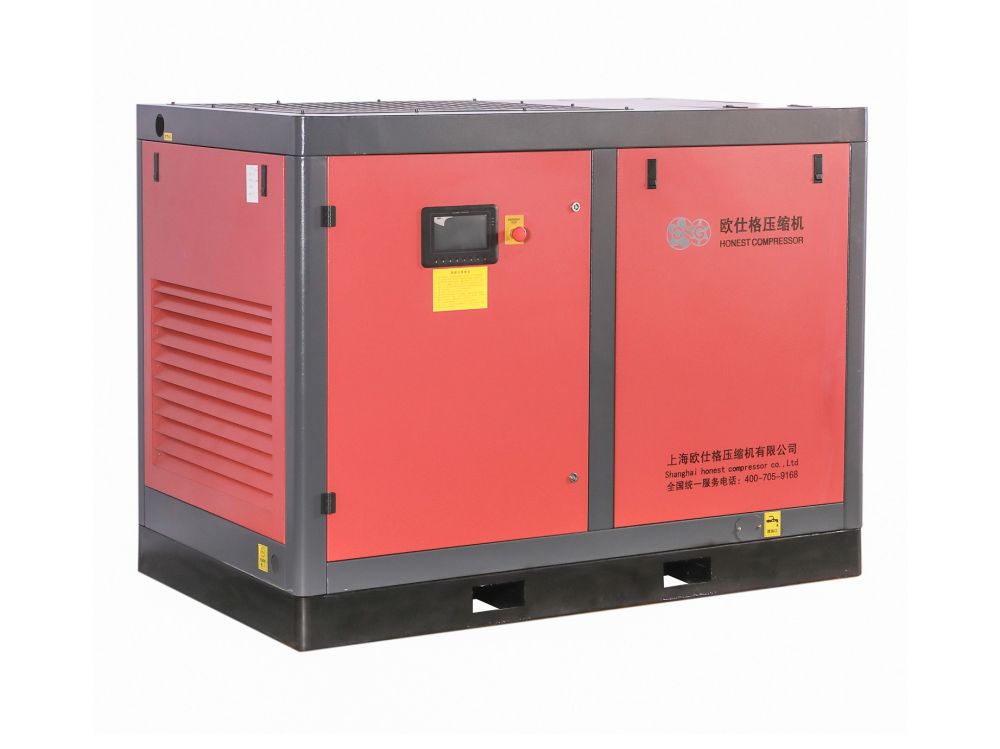
This month’s question: How important are storage receivers in a compressed air system, and how should they be used?
Ron Marshall (Winnipeg, MB, L1&2 Trainer)
Storage receivers are an essential part of a well running and efficient compressed air system. Too often we find a system with rapidly cycling compressors and sudden pressure fluctuations caused by the lack of adequate system storage capacity.
In years gone by, the rule of thumb was to install about one gallon of storage capacity for each cfm of trim compressor capacity (trim compressors take partial load, base compressors run at full load). But now, after many years of experience, we are finding there needs to be storage levels of between three and five gallons per trim cfm, and sometimes more, depending on the characteristics of the system.
I jokingly tell my clients that if a visitor to your compressor room doesn’t do a double take when they see your main storage receiver, it is probably too small. Having adequate storage in the compressor room, both wet and dry, makes it much easier to logically and efficiently control the compressors as the storage slows down pressure fluctuations substantially. Make sure you have adequate receiver capacity designed into your system, the bigger the better!
Paul Shaw (Berlin, CT, L1&2 Trainer)
Storage capacity in a compressed air system is very important. A constant source of debate is whether to locate the primary air receiver before or after the dryer. For a reciprocating compressor, a receiver placed after the compressor provides a pulsation dampening effect that benefits both the compressor and the system.
For all types of systems, locating the storage before the dryer reduces the moisture load by separating condensate, providing some temperature reduction from radiant cooling, and reducing the likelihood of liquid slugging if the aftercooler moisture separator trap of the compressor should fail. However, the downside is that as the receiver fills with saturated air, a large demand event could overload the dryer and cause moisture to be carried downstream.
Locating the air receiver after the dryer provides the dry air needed to accommodate large demand events without creating overloading. However, other problems can arise, such as the loss of the pressure band because of pressure drops through the dryer and filters, and compressor signal reaction. What is the optimum? Place storage before and after the dryer, using the wet receiver as the control point. This allows you to reap the benefits of both locations.
Secondary storage, located somewhere in the plant, can provide a source of compressed air for a single operation, reduce pressure drops, or help balance the system. In a stamping operation, for example, secondary storage provides for the sudden burst of air required for proper press operation. Without secondary storage, there may be a pressure drop at the machine clutch requiring larger line sizes or higher pressure, or sometimes both.
Storing air for a large pulse load may require needle and check valves. A check valve eliminates the possibility of storage being drawn off by events elsewhere in the system. Meanwhile, a needle valve controls the rate of refilling, so that a large demand event becomes a small, steady draw on the compressed air system.
The following formula is used to size a secondary receiver:
V = (T * (C - R) * Pa)/p1 - p2
Where: V = receiver volume, ft3 T = time allowed for pressure drop of 10 psi to occur (10 minutes) C = intermittent demand, cfm (100 cfm) R = rate of flow through the needle valve Pa = absolute atmospheric pressure, psia (14.7 psia) p1 = initial receiver pressure, psig (100 psig) p2 = final receiver pressure, psig (90 psig)
Proper use of secondary storage can provide many advantages and benefits and should be considered in an overall compressed air system strategy.
Chris Beals (Denver CO, L1 Trainer)
Storage is important, even for VSD compressors. One often hears that VSD compressors aren’t damaged by short cycling, don’t need storage, and produce air instantaneously upon starting. The truth is that short cycling has in the past damaged shaft seals and pumped the oil out of VSD compressors. Depending on when a VSD compressor operating in start/stop mode blows down, it can take 10-25 seconds for it to reach its full capacity after it gets the signal to start.
This causes problems if there is a lack of storage. Therefore, a system with a VSD compressor needs adequate usable storage, which allows the VSD unit to start and load, and prevents short cycling of either the VSD or constant-speed compressor(s).
In a multiple compressor system using a VSD trim compressor, the required usable storage is determined by the control band, the acceptable pressure decay, and the difference between the capacity of the constant-speed compressor and the turndown of the VSD compressor. Two ways to increase the usable storage are to install more volume or increase the compressor control band. However, in most cases, large pressure swings caused by a wide band are undesirable.
When deciding whether to install the compressor room storage, remember that an air receiver doesn’t need an electric cord. For more information see the Plant Services article Storage Volume for Air Compressors.
Mark Ames (St. Louis MO, L1 Trainer)
A compressed air system owner should consider both wet and dry storage. Typically, wet storage is omitted in most industrial systems, but in some cases, there is only wet storage and no dry receivers.
Some arguments against having only wet side storage:
One argument for wet side storage:
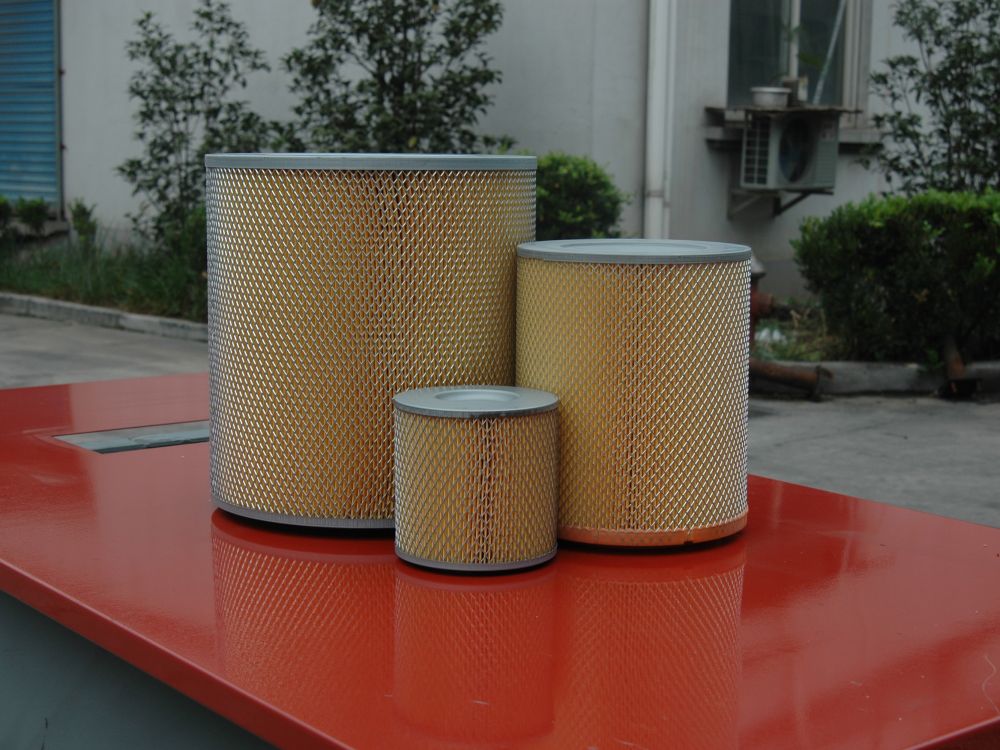
Air Dryer Working The mission of Compressed Air Challenge is to promote energy and operational efficiency in compressed air systems for industry through information and training, leading end users to adopt efficient practices and technologies while leveraging collaborative cooperation among key stakeholders. To carry out its mission, CAC maintains a group of 20 highly qualified and experienced instructors who are available to deliver its various product-neutral training offerings through in person or online training delivery. To learn more about upcoming training opportunities visit the CAC calendar.