Fiber concrete reinforcement can be a cost-effective, durable and even sustainable alternative to conventional steel like rebar and wire mesh. Can synthetic fibers compete “head-to-head” with steel? Let's talk about it.
As the demand for more sustainable construction grows and raw material shortages like steel continue to be a challenge, fiber-reinforced concrete has become an increasingly popular choice for flatwork and elevated construction—from precast and ready-mix concrete to shotcrete. Active Material
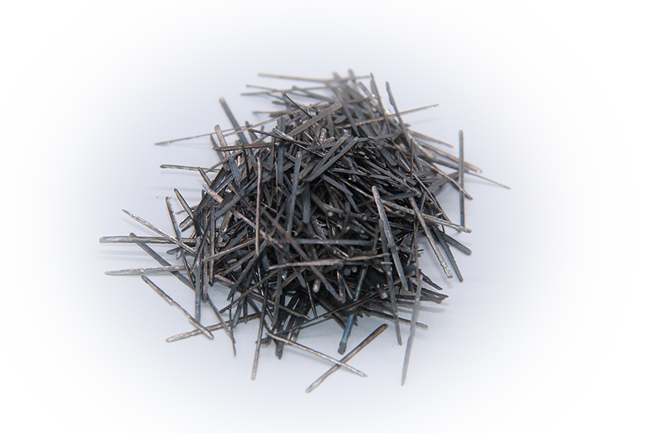
Fibers make concrete significantly more resistant to cracking from plastic and drying shrinkage, leading to a highly durable end product with a longer lifespan. Some fiber types can even greatly reduce construction time and, in some applications, eliminate the need for conventional steel.
Regarded as a cost-effective, durable and even sustainable alternative to conventional steel like rebar and wire mesh, fiber-reinforced concrete boasts a variety of benefits: Macrofiber provides three-dimensional reinforcement against cracking The Euclid Chemical Corporation
Synthetic macrofiber reinforcement The Euclid Chemical Corporation Micro-synthetic fibers provide superior resistance to plastic shrinkage cracking over welded wire, but aren’t resistant to further crack width openings caused by drying shrinkage, structural load or other forms of stress. However, they should be regularly specified in any concrete type to improve cracking resistance, spall protection, freeze-thaw durability and homogeneity of concrete during placement. Microfibers are available in 1/25” – 3/4” (12 – 19 mm) lengths, with dosage rates varying from 0.5 – 1.5 lbs/yd3 (0.3 – 0.9 kg/m3) depending on the fiber product and application type.
Macro-synthetic fibers not only provide resistance to plastic shrinkage but also enhance concrete’s durability, toughness and limited structural capacity when properly designed. Dosed at amounts equivalent to conventional reinforcement, these fibers are distributed three dimensionally throughout the concrete section.
Typical steel fiber reinforcement The Euclid Chemical Corporation Macro-synthetic fibers can be likened to the use of steel fibers, but are usually easier to place and finish due to their lighter weight, non-corrosive nature and high pumpability. Macrofibers are typically 1 1/2” to 2” (38 – 50 mm) in length, with dosage rates varying from 3.0 – 15 lbs/yd3 (1.8 – 9.0 kg/m3) depending on the fiber product and application type.
Can synthetic fibers compete “head-to-head” with steel? Absolutely. Macrofibers offer durability and residual strength capacity equivalent to steel. Assuming an adequate fiber design is performed, macro-synthetic fibers generally require 5-10 times less weight of material compared to steel, streamlining on-site handling and storage. They are also non-magnetic and non-corrosive, making them ideal for exterior pavements where aesthetics and safety are a concern. Since concrete containing macrofibers is mixed, the fiber also becomes somewhat pliable and not nearly as abrasive to pumping lines and equipment.
Macrofiber reinforcement provides cost savings over rebar and welded wire The Euclid Chemical Corporation
Providing concrete floors with early-age cracking resistance, fiber reinforcement can be used to replace conventional steel for temperature/shrinkage crack control and limited structural applications. The three-dimensional reinforcement offered by macrofibers also offers greater abrasion, fatigue and impact resistance while increasing service life through enhanced durability.
Additionally, the concrete matrix’s increased tensile capacity can reduce overall shrinkage stresses, which allows for increased joint spacing. There are successful examples and significant industry research that support the increase of control joint spacing in floor designs with macro-synthetic and steel fibers. This is typically combined with improved concrete mix designs using advanced chemical admixtures as well as proper placement and curing practices.
Some fiber manufacturers have also experimented with joint-free floors. To extend joint spacing beyond traditional construction practices, there are many factors that must be considered. Low water-to-cement ratio, lower cement content, and shrinkage reducing and/or compensating admixtures with adequate curing yields strong durability with reduced risk for curling and shrinkage cracks. Other factors such as proper subgrade preparation, placement, saw-cut depth, curing time and exposure conditions must also be evaluated.
Concrete pavement with macro-fiber reinforcement The Euclid Chemical Corporation It is highly recommended to conduct testing and verification prior to a flooring construction project to ensure engineering and specification requirements are met. This is typically done by conducting shrinkage tests on the proposed concrete mix design to establish general shrinkage characteristics, which lead to the discussion of potential joint spacing measurements.
Fiber-reinforced concrete is also a cost-effective, sustainable solution for resurfacing and rehabilitating existing pavements and bridge decks. In fact, many state DOTs and other transportation agencies are promoting macrofibers over conventional steel and developing performance-based specifications for pavement overlays and full-depth replacement systems to increase service life and reduce long-term maintenance costs.
Macro-synthetic fibers significantly reduce or even completely eliminate the expense and installation time of conventional reinforcement, while producing concrete pavements that are easily placed with less environmental impact on the jobsite.
Macro-synthetic fibers can also be used as an alternative to steel reinforcement with nearly any concrete wall application. The dosage rates are based on strength-to-strength calculations supported by standardized test methods and industry practices. This significantly reduces time and labor costs, while producing more durable concrete. These fibers can also provide the same strength capacity as steel in wall applications such as foundations and retaining walls.
Macro-fiber reinforcement can be used as a cost-effective, sustainable solution for buildings constructed with insulated concrete form (ICF) wall systems, which have historically been reinforced by steel rebar engineered to resist forces from soil, wind and other loading conditions. Dosed correctly, macrofibers eliminate rebar in ICF walls for significant time and cost savings.
Typical fiber-reinforced concrete surface finish The Euclid Chemical Corporation
Fiber used insulated concrete form construction The Euclid Chemical Corporation Adding fibers often reduces the slump of a concrete mix, which measures the workability of fresh concrete during placement. This is likened to adding more ingredients to the mix and, therefore, requires more fluid to maintain an apparent slump—hence the appearance of workability loss. Microfibers, used at typical dosages, generally only decrease slump slightly and don’t require significant changes to maintain placement characteristics. Yet, macro-synthetic and steel fibers can affect the workability of concrete in a more significant way, depending on fiber type and dosage.
To improve the workability of fiber-reinforced concrete, the ACI 544.3 standard offers recommendations and guidance to potentially modify the mix design. Additionally, the use of chemical admixtures like superplasticizers or water reducers increase the workability of concrete without adding water. It is recommended that trial batches are performed to ensure mixture workability.
Factors such as fiber material type, architecture, dimension and dosage may affect the surface finish of fiber-reinforced concrete, as well as the required surface-finishing method that is used. Stiff or rigid fibers typically have a greater tendency to protrude up through the slab than flexible fibers.
Proper external vibration is another key factor when finishing fiber-reinforced concrete. The general recommendation is to use the same finishing techniques and approximate timing as conventional concrete. When casting samples for testing, no internal vibration within the molds can be used. Synthetic fibers may delay bleed water at the surface, which impacts finish timing on larger slabs.

Alumina Grinding Media There are many broom finishing tips that minimize surface appearance, such as brooming in one direction or using specific broom bristles to align surface fibers. If necessary, a torch can burn off synthetic fibers on a concrete surface—but should not be used until all desired hardened concrete properties are achieved. When finishing industrial, commercial and warehouse floors where high dosage levels of macro-synthetic and steel fibers are used, a laser or vibrating screed is usually recommended.