Industrial robots play an essential role in manufacturing, from assembly, to pick-and-place, to packaging. One of the major risks of robotics — and what OEMs seek to mitigate — is uncontrolled or non-commanded motion by a robot. Most electric robots today incorporate servomotors for direct-drive operation. This approach largely eliminates the need for clutches, but robots still need brakes, both to apply holding torque once the motor moving the joint has stopped, and to provide dynamic stopping in the event of emergency.
Even among industrial applications, the requirements placed on robots vary significantly. In addition to key performance parameters such as torque, backlash, and response time, robotic applications need to meet tight tolerances for characteristics like weight, diameter, and mounting configuration (such as large through bore). This differs not just from use-case to use-case, but also depending upon where along the robot arm a given brake is installed. Fortunately, OEMs have multiple options from which to choose. Audio Control Equipment Spare Parts
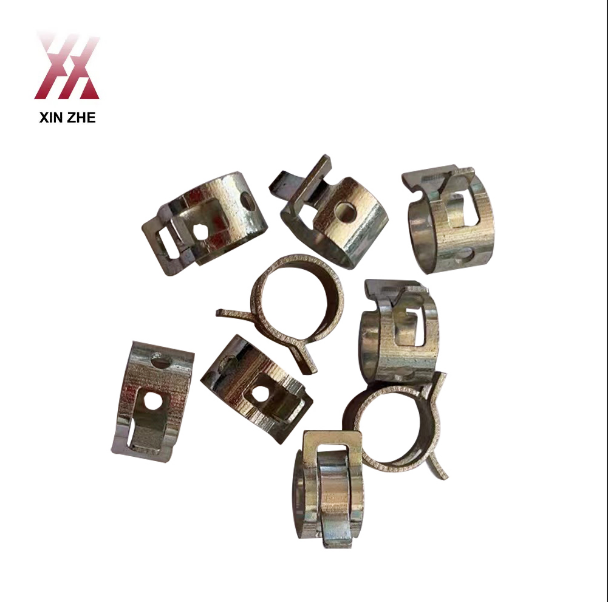
The brakes most commonly used in robot applications can be classed as spring-engaged or permanent-magnet-engaged types. Spring-engaged brakes can be further divided by their method of generating stopping/holding torque into friction type and tooth type.
The key elements of a spring-engaged friction brake are the field coil, which is fixed to the machine frame or a backstop; the armature; the friction disk; and the pressure plate (Figure 1). Brakes of this type are typically, but not always coupled to the shaft with a hub, which is fixed to the shaft with a set screw. In the power on condition, the field coil generates an electromagnetic field that attracts the armature, compressing the springs and opening up an air gap between the armature and the friction disk. This allows the friction disk to rotate freely with the hub, shaft, and load.
When power is off, the force of attraction between the field coil and armature falls to zero. The spring between the armature and the magnet body pushes the armature into contact with the friction disk. The friction disk is squeezed between the pressure plate and armature, transmitting torque and stopping/holding the disk, hub, and shaft.
The performance and attributes of a spring-engaged friction brake can be tuned to the application. Materials with low coefficients of friction work well for dynamic applications, while high-coefficient materials are better suited to holding brakes. OEMs can select materials tailored for special environmental conditions such as vacuum, wet environments, and even applications involving oil.
A spring-engaged tooth brake is based on a field coil, a toothed armature, and a toothed output plate attached to the load (Figure 2). When power is on, the field coil attracts the armature, compressing the springs and opening up an air gap between the armature and the output plate. This allows the load to turn freely. In the power off case, the field coil releases the armature. The springs press the armature against the output plate so the teeth engage and the load is stopped/held.
Tooth profiles can be modified to adjust performance. The standard tooth profile yields a brake that is strong, durable, and bidirectional (Figure 3). It can engage while the load is in motion at low RPM.
Widening the tooth angle enables the brake to engage at higher speeds. This tooth design is limited in the amount of torque it can handle. When the torque rises too high, the brake can slip, making it useful for overload torque control. This so-called overload tooth profile always disengages under load when the system switches directions.
The self-locking tooth profile is closer to a square-wave shape. It can transfer much more torque than the other types of profiles. It will not disengage under load when the system switches directions.
A third type of brake commonly used in robotics is the permanent-magnet friction brake. This type consists of a permanent magnet, field coil, armature plate, and hub. When power is off, the permanent magnet pulls the armature into contact with the friction faces, holding the shaft, hub, and load in place (Figure 4). When power is applied, the field coil generates a magnetic field of opposite polarity to that of the permanent magnet, which brings the force at the face of the armature to zero. The armature disengages from the electromagnet housing, assisted by a diaphragm spring.
The requirements of industrial applications vary widely from use-case to use-case. Key factors include torque, backlash, torque-to-diameter ratio, bore diameter, resolution, and, of course, cost.
Torque — The torque required to stop or maintain the static position of a robot depends upon a range of factors, including structure, weight, and load, and in the case of dynamic stopping torque, velocity.
In the case of a brake required to stop a robotic arm (Figure 5), we can express holding torque τh as
where r equals the moment arm, F is the load, and K is service factor, a constant that accounts for wear; it typically ranges from 1.5 to 3. Practically speaking, this expression needs to be an integral that takes into account the weight of the arm as well as the load at the end.
Backlash — Backlash is defined as the amount by which the shaft will rotate while the brake is holding. This lost motion depends upon the hub used to connect the shaft to the brake. Hub options include hex, “double D” (a shaft with flats machined on opposing sides), and toothed spline designs. It is important to note that the hub must provide sufficient clearance to enable the armature to move axially along the shaft. As a result, a spring-engaged brake will always have some degree of backlash.
Different hub designs exhibit different degrees of backlash. A D or double-D hub has the greatest amount of backlash. A hex hub performs better, but still needs clearance on each side. Backlash for spline hubs is a function of diameter, ranging from about 0.25° for small brakes (1.5” diameter) to 1° for larger units (5” diameter or above).
The level of acceptable backlash depends upon the application. An industrial pick-and-place robot assembling a multipack of lunch meats might be able to tolerate a degree or two of backlash, while a robot populating a PCB board might need to operate to better than 0.25°.
For high-accuracy, high-precision applications, permanent-magnet brakes offer zero-backlash performance. Examples include semiconductor fabrication and medical device manufacturing. For most other industrial applications, spring-engaged brakes will perform effectively and at a reasonable price.
High Torque-to-Diameter Ratio — Robots are highly space-constrained, so torque-to-diameter ratio is a key brake characteristic. The specifics of the application ultimately drive requirements, but in general, OEMs should look for the highest possible torque-to-diameter ratio. This is particularly important for the brakes used at the base of the robot arm (Figure 6). Spring-engaged tooth brakes have the highest torque-to-diameter ratio, followed by permanent-magnet friction brakes and spring-engaged friction brakes (Figure 7).
Bore Diameter — Brakes for robotic arms need through holes to permit the passage of cables, optical fiber, laser beams, and more. In general, permanent-magnet brakes provide the largest bore diameters, followed by spring-engaged tooth brakes. The bore diameter of spring-engaged friction brakes tends to be smaller as a result of the components involved, and the fact that they typically arrive as easy-to-install assemblies.
Response Time — Power-off brakes are typically used as safety brakes that engage when power fails. This purpose makes response time particularly important. Permanent-magnet friction brakes have response times on the order of 10 ms. Spring-engaged brakes tend to be slower — a 3” spring-engaged brake has a response time of between 60 and 100 ms. For cases in which the sudden drop of the robot arm could endanger personnel or damage product and equipment, a permanent-magnet friction brake is the best choice. If an arm is not likely to encounter any objects during a 100-ms move, then a spring-engaged brake provides a more economical solution.
Resolution — Robotic applications focus on highly controlled motion, so resolution should always be taken into account. Both spring-engaged friction brakes and permanent-magnet friction brakes offer infinite resolution. The resolution of tooth brakes is limited by tooth-to-tooth angle and the number of teeth per revolution.
Cost — Particularly in the industrial sphere, cost is always a major factor. In the case of robotic brakes, spring-engaged friction brakes are the most economical solution. They offer effective performance for a wide range of applications, making them the go-to solution for many systems. Permanent-magnet friction brakes are next in terms of cost. That makes them less appealing from a budgetary standpoint, so they should be reserved for applications that demand the specific set of characteristics that they offer. Finally, spring-engaged tooth brakes are most expensive as a result of the precision manufacturing required for the tooth interface.
OEMs building robotic solutions have a variety of brake options to help them achieve their desired performance. Spring-engaged friction brakes provide good general performance at an economical price point. For space-constrained equipment that requires high holding torque, spring-engaged tooth brakes are quite effective, but the tradeoff is higher cost and limited resolution. Permanent-magnet friction brakes offer wide bores and infinite resolution, as well as zero-backlash operation. Engineering teams should understand their application, review their options, and partner with their supplier to find the optimal solution.
This article was written by Rocco V. Dragone, Senior Sales/Application Engineer at SEPAC, Elmira, NY. For more information, visit here .
This article first appeared in the April, 2018 issue of Motion Design Magazine.
Read more articles from this issue here.
Read more articles from the archives here.
A Green Li-ion Battery-Recycling Method
TELEPORT: A New, Better Way to Extract Lithium
Making Hydrogen the Next Major Fuel Source for Soldiers
U.S. Army Pathfinder Program: Innovation in Makerspaces
How Much Do You Know About Predictive Maintenance?
Hydrogen’s Promising Role in Heavy-Duty Vehicles
Noise, Vibration, and Harshness Priorities for EVs
Revolutionizing Electric Mobility: Advancements in Physics Simulations and CAE Methods
Advancing Software Development for the Future of Autonomous Military Vehicles
Leveraging Today’s Extrusion Technology: Hollows and More!
Additive Manufacturing for Aerospace: Taking Your Production to New Heights
Climate-Friendly Sodium-Ion Batteries to Rival Li-ion Batteries
Answering Your Questions: Lithium-Air Battery vs. Lithium-Ion
How Much Do You Know About the History of Space Telescopes?
Comparison Between Wave Soldering and Reflow Soldering
Printed Electronics: The Future Is Flexible
Expanding Copernicus’s Earth Observation Program With Hyperspectral Imaging
Polycarbonate Seen As Top Choice for LED Lighting
Network of Robots Can Successfully Monitor Pipes Using Acoustic Wave Sensors
The Modern Industrial Workhorse: PID Controllers
The Basics of Encoder Selection
Photonics West 2024: 5 New Technologies on Display This Year
Smart Sensor Technology for the IoT
Networking the IoT with IEEE 802.15.4/6LoWPAN
Leveraging Today’s Extrusion Technology: Hollows and More!
Laser Beam vs. Electron Beam Welding Which process works best for what?
A Precision Arm for Mini Robots
Mechanical Carbon Materials for Aircraft Seal Applications
Brushless Motors for In-Tank Fuel Pumps
Here's an Idea: A New Minimally Invasive Approach to Spinal Cord Injury
Here's an Idea: Human Factors in Drug Delivery
Here's an Idea: Powerful Sensors for the Eye
By submitting your personal information, you agree that SAE Media Group and carefully selected industry sponsors of this content may contact you and that you have read and agree to the Privacy Policy.
You may reach us at privacy@saemediagroup.com.
You may unsubscribe at any time.

Stamped Mold © 2009-2024 SAE Media Group