Clean, burr-free cutting is fundamental to competitiveness for a shop that specializes in micro-machining complex geometry from some of the softest materials in the industry. #micromachining
The shop’s staffers rely on patience, experience and a steady hand to machine geometry almost too small to see on equipment that would be just as suitable for more conventionally sized parts. Here, Richie Fernandez, machinist, indicates a drill on the shop’s Hardinge SV 200 lathe. Axis Machining
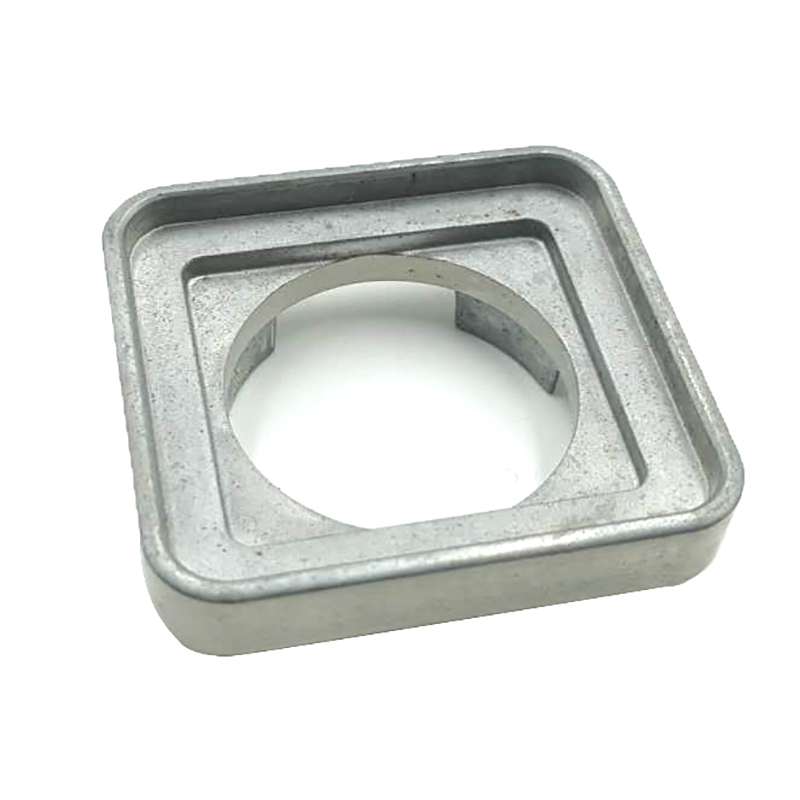
Given the prevalence of features like the slots in the sides of this Torlon 4203 part, milling and drilling capability is common to all of the shop’s turning machines.
Another view of the slots in the Torlon 4203 part.
This Ultem component’s washer-like geometry makes it particularly prone to burrs. Given the central hole, a cut-off tool that isn’t sufficiently sharp could create enough pressure to break the part off the rest of the stock, thus creating a semi-circular, ribbon-like burr around the edge of the ID, before it has a chance to shear all the way through.
The subspindle on the shop’s Citizen A16 Swiss-type lathe approaches very close to the main spindle when picking off small parts. To ensure clearance, this toolholder has been ground narrower near the cutting edge. The insert has also been modified to ensure a clean break from the rest of the stock.
Shown here mounted on a wire, this polytetrafluoroethylene (PTFE) part prompted the shop to increase attention to the cleanliness of its coolant. Measuring only 0.015 inch, the part is virtually indistinguishable from chips leftover from other jobs without sufficient coolant filtering.
Small parts call for small tools, such as the 0.023-inch drill used to cut a hole through the length of this Torlon 4203 component. Recently, the shop added high-pressure coolant to its A16 Swiss-types and invested in through-coolant tooling to help ensure effective chip evacuation.
At East Coast Precision, organized, tidy workstations are reflective of the calm, patient mindset required to work with small parts. Toolmaker’s microscopes like the one shown here are placed strategically on tables like this throughout the shop, along with quality policies, travelers for specific jobs and other reference information.
After eight years at East Coast Precision Manufacturing, Chris Marchand knows a thing or two about micro-machining plastics. Having specialized solely in this work since its inception in 2006, the shop has carved a niche for itself in small, complex geometry that other manufacturers can’t or won’t quote. Asked for specifics on how the shop leverages its deep knowledge of machining everything from acetal, acrylic and polytetrafluoroethylene (PTFE) to trademarked materials like Teflon, Ultem and Torlon, Mr. Marchand repeatedly returns to one particular topic. “The more I think about it, the more I realize just how focused we are on controlling chips,” he says.
Even the hardest plastics are prone to bend and stretch rather than break when subjected to force, he explains. As a result, turning and milling often create long, stringy chips that can adhere stubbornly to the rest of the stock; gum up cutting edges; and wrap around the part, the tool shank or anything else they happen to catch as they peel away. Beyond problems during machining, effective chip control is critical for preventing burrs, which can significantly increase overall manufacturing time for the shop’s tiny plastic parts.
Given that this challenge is fundamental to every job, chip control is a fundamental part of planning every manufacturing sequence. In fact, operations and tools are often dedicated specifically to that purpose. Not just any tools will do, either. The shop routinely modifies geometries on an in-house grinder to ensure material breaks away cleanly. For the same reason, all cutting tools must be exceedingly sharp. Attention to coolant delivery is also critical to ensure waste material flushes away from the cutting zone.
Like seemingly everything else going on at this Chester, Connecticut, shop, these chip control strategies are rooted in basic concepts, but they’re applied with the benefit of extensive, plastic-specific expertise. Indeed, a look at the 5,600-square-foot shop floor is enough to reveal that both kinds of knowledge are the true linchpins of East Coast Precision’s success. After all, workhorse machines like the shop’s seven FANUC RoboDrill VMCs may be fast and perfectly capable of meeting the ±0.005-inch tolerances required for most work, but they’d also be at home in any number of other machine shops. The case is the same for the 12-employee company’s Hyundai and Hardinge slant-bed lathes with live tooling attachments. Indeed, the only obvious evidence that East Coast Precision is set up specifically for small, plastic work consists of the parts themselves, the presence of two Citizen A16 Swiss-type lathes, cutting tools as small as 0.02 inch in diameter, and fine-screen parts catchers.
That’s not to say that keeping up with technology isn’t important to the shop—on the contrary. The shop prioritizes technology that enables consolidating operations in fewer setups, as evidenced by the Swiss-types, the live tooling and its most recent purchase, a Miyano BNA42S turn-mill with a main spindle and fully controllable C-axis subspindle. Nonetheless, Mr. Marchand emphasizes that knowing exactly how any given material will break apart during machining has had a far greater impact on the shop’s ability to handle geometry almost too small to see with equipment commonly used for conventionally sized parts. He also emphasizes the importance of fundamentals: specifically, a solid setup, a steady hand and a patient mind. More than anything else, East Coast Precision’s competitiveness depends on both deep knowledge and best-practice, common-sense manufacturing.
When it comes to raw shopfloor efficiency, nowhere is this combination more important than chip control, he says. The following provides a brief look at the basic concepts behind the shop’s go-to strategies for avoiding defective parts, chip “bird nests,” time-consuming deburring operations and other issues that can push back delivery dates.
Chip control begins with the right parameters, and programmers draw extensively on past experience when determining which feeds and speeds will result in a clean cut. Although material isn’t the only variable in this exercise, it is particularly significant for East Coast Precision because the range of plastics machined here is so broad, and each behaves differently. Generally, softer materials tend to present more problems than harder ones because chips don’t break as cleanly from the stock, Mr. Marchand says. Using higher feeds and speeds in these materials can help to, as he puts it, “create a fat chip and carve it off before it has a chance to screw anything up.”
Making deburring part of the process. Hobby knives are among the most frequently used tools at the shop, Mr. Marchand says. Whether for reasons of aesthetics or function, most parts machined at East Coast Precision require smooth surfaces. Unfortunately, conventional deburring methods like tumbling tend to be ineffective, because dangling plastic tends to “flap around” rather than break, he says. Mechanical deburring can also damage more sensitive plastics. As a result, some parts leave no other option but to spend hours whittling away manually at residual chads of material.
However, this laborious task can often be avoided with strategic tool paths, Mr. Marchand says, noting that programmers attempt to “keep the burr in front of the cutting tool” whenever possible. Beyond that, a look at any of East Coast Precision’s part programs is likely to reveal cutting paths doubling back on one another, and he insists this isn’t wasted motion. With limited deburring options, having one tool follow another to “clean up” the material in its wake is often more cost-effective than manual trimming, and it tends to have minimal impact on overall cycle time anyway.
Leveraging the right tool geometry. Many of the aforementioned “cleanup cutters” are standard offerings that have undergone modifications on the shop’s Deckel S0 benchtop tool grinder. However, imparting chamfers and other geometries that help remove burrs is just one of many purposes of customizing tool geometry. For instance, a standard, 0.019-inch grooving tool might be ground to 0.011 inch to cut a narrower channel, or part of a boring bar might be ground away to avoid interference with a taper at the back of a blind hole. Of course, other geometries are far more involved, and Mr. Marchand says those provide a competitive edge.
In any case, one reason the grinder gets so much use is that tool designs that work well in other materials don’t necessarily translate to plastics. This also leads the shop to prioritize simple geometry in its standard cutters, Mr. Marchand says. For instance, chip-breakers are a no-no because they can exacerbate the tendency of soft, stringy material to stretch and twist as it peels away from the stock. All of the shop’s milling and turning tools also tend to have a neutral rake angle. Keeping the edge as perpendicular to the material as possible helps prevent flexing the plastic too far away from the cut and encouraging longer spirals, as might happen with a negative rake, or drawing it inward and gumming up the cutting zone, as might happen with a positive rake. In a turning operation, either scenario could also result in unwanted taper and poor surface finish, Mr. Marchand says. With few exceptions (Fiberglass, for instance), the shop never buys coated tools because there’s simply no advantage, he adds, explaining that plastics aren’t hard enough on tools or machines to justify it.
Keeping tools sharp. The prevalence of customized and slightly modified tool geometries isn’t the only reason why East Coast Precision’s benchtop grinder is in high demand among employees. Tool sharpness is a top priority, Mr. Marchand says, even to the point that the shop is known to sharpen brand new cutters right out of the box, before they’re ever used. To the same end, employees performing setups are often found peering through the eyepieces of 30X-magnification toolmaker’s microscopes to ensure tools are sharp before putting them in machines. Tools are also changed frequently to ensure they stay as sharp as possible. Finally, dull tools are always a chief suspect when something goes wrong with a process.
Sharp tools are so important for two reasons. First, the smaller the part, the greater the potential impact of a dull tool that “pushes” material rather than shearing cleanly through it. Second, that kind of pushing is far more likely to happen in plastic than in even the softest metal. “Even in harder plastics, there might be little pits where a dull tool has torn off material as opposed to slicing it,” Mr. Marchand says. “These types of surface finishes are unacceptable for our work.”
Taking full advantage of coolant. The benefits of coolant go beyond removing heat from the cutting zone. It is also an essential part of chip control. Although that’s true for any shop, East Coast Precision has taken extra steps to ensure that the coolant delivery systems on its two Swiss-type lathes play this role as effectively as possible.
The most obvious addition is extra delivery lines for the shop’s water-based coolant. (Water-based coolant is generally preferred to oil formulations, which tend to leave difficult-to-clean residue on plastic parts, Mr. Marchand notes.) Beyond increasing coolant volume—and thus, the likelihood of flushing out stray chips—extra lines provide more options for controlling coolant direction. Mr. Marchand says those options come in particularly handy for custom tool geometries that are prone to deflecting chips directly into the feed, another cutter in the tool magazine or any other undesirable location.
The shop didn’t stop there. Both Swiss-type machines are fitted with a Loc-Line magnetic manifold kit that mounts to the Y-axis structure to keep coolant hoses in the same position relative to the work as the machine runs. Meanwhile, aftermarket valves enable operators to switch off coolant nozzles individually, Mr. Marchand says, whether to better direct flow or to take advantage of the resulting pressure increase in the rest of the lines.
Perhaps the most significant change of all has been the addition of high-pressure coolant. The challenges plastic presents for chip control make holes with extreme length-to-diameter ratios particularly difficult to machine. That difficulty, in turn, makes these holes a particular specialty for East Cost Precision, Mr. Marchand says. For years, the shop has been refining the use of techniques like peck drilling, in which rapidly oscillating the drill helps prevent chips stuck in the flutes from rubbing against the sidewall and scarring the material. However, with coolant pressures ranging to 2,000 psi (compared to only 40 psi before) and through-coolant cutting tools, such techniques are even more effective and might not even be required.
Keeping clean. Finally, Mr. Marchand emphasizes that keeping coolant filtered and machines clean is imperative when working with small parts. The component on page 93, for instance, proved difficult to distinguish from chips caught by the fine-screen parts catcher on one of the Swiss-types. One step taken as a result is to make it more of a priority to routinely ensure coolant is filtered and machines are clean. That boils down to basic housekeeping. As such, it serves as evidence that even the deepest expertise goes only so far in ensuring chip control (or achieving any other goal, for that matter) without common sense and a solid grasp of fundamentals.
Consider these alternatives when conventional drilling can't do the job.
Old-world craftsmanship combines with precision machining on a vertical machining center and Swiss-type lathe to produce some of the only U.S.-made mechanical wristwatch movements.
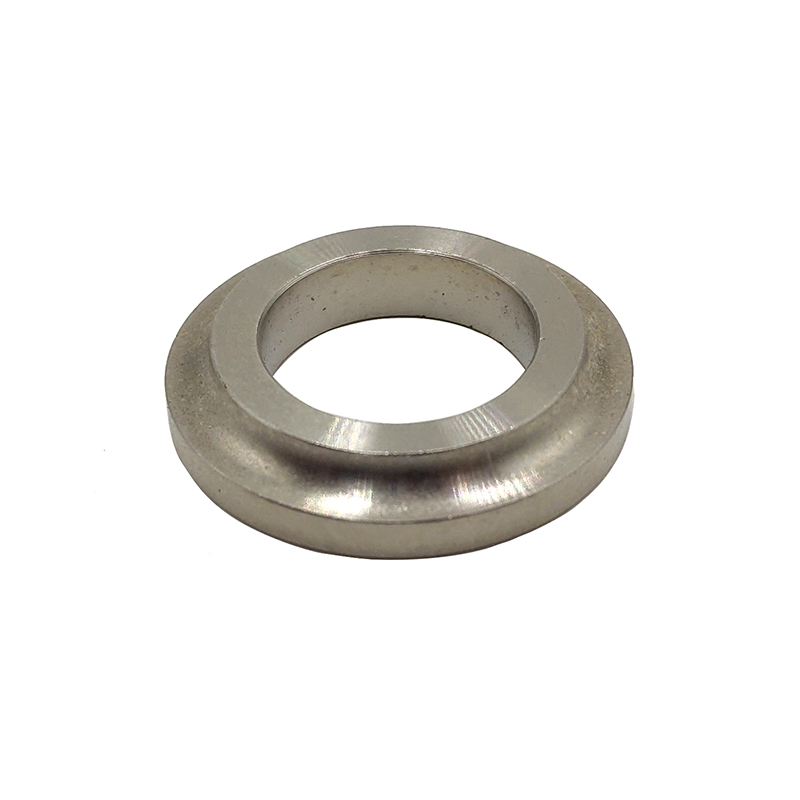
Cnc Machining Metal Instead of shipping small components from overseas, a watchmaker was able to accommodate increased demand by purchasing a used five-axis machining center.